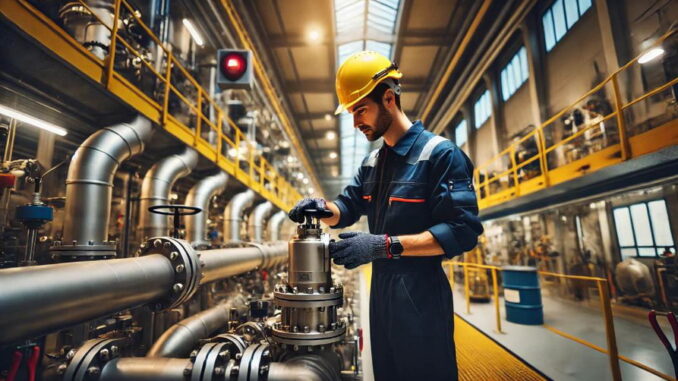
La manutenzione degli impianti industriali rappresenta un aspetto irrinunciabile per qualunque azienda che intenda salvaguardare la salute del proprio personale e garantire la continuità delle attività produttive. Trascurare i controlli periodici, infatti, significa esporre i lavoratori a rischi concreti di guasto e incidenti, con conseguenze potenzialmente molto serie. In questo articolo vedremo perché un piano di manutenzione ben strutturato e un’adeguata cultura della sicurezza rivestono un ruolo fondamentale nel creare un ambiente di lavoro più protetto ed efficiente.
La manutenzione degli impianti industriali rappresenta un aspetto irrinunciabile per qualunque azienda che intenda salvaguardare la salute del proprio personale e garantire la continuità delle attività produttive. Trascurare i controlli periodici, infatti, significa esporre i lavoratori a rischi concreti di guasto e incidenti, con conseguenze potenzialmente molto serie. In questo articolo vedremo perché un piano di manutenzione ben strutturato e un’adeguata cultura della sicurezza rivestono un ruolo fondamentale nel creare un ambiente di lavoro più protetto ed efficiente.
Rischi associati alla mancanza di manutenzione: infortuni e incidenti comuni
In ambito industriale, la mancanza di manutenzione è spesso la causa primaria di numerosi inconvenienti che possono sfociare in situazioni di pericolo per i dipendenti. Le attrezzature usurate o difettose incrementano notevolmente il rischio di cedimenti, surriscaldamenti o fughe di sostanze nocive, mettendo a repentaglio sia la salute del personale che la stabilità dell’intero processo produttivo. Al tempo stesso, una gestione superficiale della manutenzione tende ad aumentare i tempi di fermo macchina a causa di rotture improvvise, con conseguenti perdite economiche.
I rischi più comuni
Tra gli infortuni più comuni troviamo quelli dovuti alle esplosioni o agli incendi, specialmente in settori dove si impiegano materiali altamente infiammabili, come vernici o solventi chimici. L’accumulo di grasso e polveri senza un’adeguata pulizia può favorire la formazione di miscele pericolose, mentre l’utilizzo di valvole, raccordi o tubi danneggiati facilita fuoriuscite o sbalzi di pressione capaci di innescare incidenti gravi.
Da non sottovalutare, inoltre, sono i pericoli legati ai crolli strutturali: le vibrazioni continue di macchinari pesanti e la mancanza di ispezioni periodiche possono minare la stabilità degli edifici, generando crepe e cedimenti che si ripercuotono sull’intero stabilimento.
Altri rischi rilevanti
Un altro rischio, spesso trascurato ma altrettanto rilevante, riguarda le cadute o gli scivolamenti provocati da pavimentazioni dissestate o bagnate che non sono indicate dall’apposita segnaletica: situazioni che, seppur appaiano meno drammatiche, possono avere ripercussioni importanti, come infortuni muscolari e fratture.
In definitiva, un’azienda che trascura la manutenzione degli impianti espone i propri dipendenti a un ventaglio di possibili incidenti che, a lungo andare, risultano molto più onerosi di qualunque strategia preventiva.
Componenti chiave da controllare: raccordi, valvole, tubi e manometri
Quando si parla di manutenzione, non tutte le parti di un impianto hanno la stessa rilevanza. Alcune componenti, per la loro funzione o per l’intensità di sollecitazioni a cui sono sottoposte, meritano un’attenzione particolare.
I raccordi
Tra questi elementi figurano i raccordi, che collegano diverse sezioni di un impianto: se un raccordo cede o si corrode, possono verificarsi perdite di liquidi o gas ad alta pressione con un impatto immediato sulla sicurezza dei lavoratori.
Le valvole
Analogamente, le valvole svolgono un ruolo cruciale nel regolare i flussi di aria, acqua o sostanze chimiche e nel mantenere valori di temperatura e pressione sotto controllo. Un malfunzionamento di una valvola di sfogo, ad esempio, può causare sovrappressioni impreviste e pericolose esplosioni.
I tubi
I tubi rappresentano letteralmente le “arterie” di molti processi industriali, trasferendo fluidi e gas all’interno di un circuito talvolta complesso. Questi componenti sono spesso soggetti a fatica meccanica dovuta a continue variazioni di temperatura e pressione, nonché all’azione di sostanze chimiche aggressive. Un tubo danneggiato rischia di rompersi e di rilasciare sostanze tossiche o infiammabili all’interno dell’ambiente di lavoro.
I manometri
Infine, i manometri forniscono informazioni essenziali sullo stato di pressione di un sistema: avere dati errati, a causa di uno strumento starato o rotto, significa prendere decisioni operative sbagliate che potrebbero tradursi in guasti catastrofici.
È dunque evidente che il controllo periodico di questi elementi non sia da prendere sotto gamba, essendo a tutti gli effetti un fattore strategico che incide in modo diretto sull’affidabilità dei macchinari e sulla sicurezza complessiva dell’impianto. Allo stesso tempo, è essenziale investire in componenti di qualità, realizzati con standard elevati e materiali certificati, così da ridurre la probabilità di cedimenti e valorizzare le competenze acquisite dal personale.
Procedure di manutenzione preventiva: linee guida e frequenza degli interventi
Per scongiurare guasti improvvisi e assicurare che gli impianti funzionino in modo ottimale, è fondamentale programmare una manutenzione preventiva. Tale strategia implica la pianificazione di controlli e sostituzioni prima che si verifichi il danno, basandosi su protocolli ben definiti.
Frequenza degli interventi
In primo luogo, occorre stabilire la frequenza degli interventi: l’ideale è procedere con ispezioni regolari, la cui cadenza dipende dalla tipologia di processo, dal livello di automazione e dal contesto ambientale.
Programma di manutenzione
Un accurato programma di manutenzione include anche:
- Test specifici, come verifiche di tenuta e prove di funzionalità delle valvole di sicurezza.
- Misurazioni della pressione in diversi punti critici della linea.
- Aggiornamento di registri o software di gestione, in cui annotare i risultati di ogni ispezione.
Questa documentazione consente ai responsabili di individuare trend di usura ripetitivi e organizzare interventi mirati, evitando la compromissione di intere sezioni dell’impianto.
Piano d’emergenza
Parallelamente, è indispensabile definire un piano d’emergenza: in caso di allarmi, fughe o blocchi di produzione, le procedure devono chiarire come:
- Isolare il problema.
- Mettere in sicurezza i lavoratori.
- Contattare immediatamente i soccorsi esterni, se necessario.
Esercitazioni periodiche
A seconda dell’azienda, le linee guida possono prevedere esercitazioni periodiche che simulino situazioni critiche, così da garantire che il personale sappia esattamente come comportarsi.
Formazione dei dipendenti: importanza della formazione continua sulla sicurezza
Le migliori procedure di manutenzione rischiano di risultare inefficaci se il personale non è adeguatamente formato. Gli operatori dovrebbero conoscere a fondo i macchinari su cui lavorano e comprendere quali siano i comportamenti più idonei a evitare malfunzionamenti e incidenti. È indispensabile organizzare corsi periodici – teorici e pratici – che insegnino a identificare i segnali d’usura e le anomalie, nonché a intervenire tempestivamente per ridurre i rischi.
Collaborazione tra reparti
In questa prospettiva, la collaborazione tra reparti è fondamentale: i tecnici di manutenzione non possono operare isolatamente, ma devono interfacciarsi con gli addetti alla produzione e con chiunque gestisca fasi chiave dell’impianto. La comunicazione agevola la segnalazione di eventuali guasti e favorisce la condivisione di buone pratiche, affinché ciascun operatore si senta parte attiva di un processo virtuoso di prevenzione. Durante la formazione, si insiste anche sull’uso corretto dei dispositivi di protezione individuale (DPI), sulle norme di sicurezza interna e sulle procedure di lockout/tagout, che consentono di isolare in maniera sicura i macchinari prima di effettuare riparazioni o manutenzioni.
Investire nella manutenzione per garantire un ambiente di lavoro sicuro
In definitiva, la manutenzione degli impianti industriali è un fattore determinante per conciliare produttività e sicurezza sul lavoro. La cura metodica dei macchinari, l’uso di componenti certificati e la formazione continua del personale rappresentano gli elementi essenziali di un sistema preventivo che protegge i lavoratori e sostiene la crescita aziendale nel tempo. Ridurre gli incidenti significa infatti salvaguardare vite, migliorare la reputazione e ottimizzare l’intero ciclo produttivo, con vantaggi concreti sia dal punto di vista economico, sia da quello umano.
Commenta per primo